飛騨の匠とはHIDA NO TAKUMI
飛騨の家具
「飛騨の家具」ものがたり
「飛騨の家具」の源をたどると、1300年前の奈良・平安時代までさかのぼることができる。時の中央政府は都造りのために、遠く離れた飛騨国に優れた木工職人の供給を依存し、「飛騨の匠」として宮殿や寺院の造営という一大国家事業のために、特別な法律を作ってまでも必要とされた技術集団の存在があった。平安期の記録には、国家的儀式や行事を執り行う大極殿や、天皇のもてなしの施設である豊楽殿などの造営にまつわる話が登場する。877(元慶元)年平安宮大極殿再建工事が始まり、「飛騨の匠60人へ賜餐(しさん=高貴な人から食事を賜る)があった」。 879(元慶3)年には、大極殿完成「飛騨の匠20人ほどが祝宴を賜る」など、平安時代の歴史書『三代実録』には幾つかの記録が残されている。
「飛騨の匠」の派遣は平安時代末期ころに終演をむかえるが、他国に類を見ない、優れた木工職人を派遣した国として位置づけられ「飛騨の匠名工伝説」が全国各地に残っており、現在も語り継がれている。この卓越した匠達の技は明治~大正〜昭和〜平成〜令和の匠へと脈々と受け継がれ、飛騨の家具作りの原点として今日に至っている。
また、「飛騨の家具」の歴史は、日本の椅子のデザインの歴史であると同時に、技術の歴史でもある。技術なしでは、新しい造形は生まれてこなかった。ここでは「飛騨の家具」発祥の歴史をたどりながら技術という視点からも考察してみる。
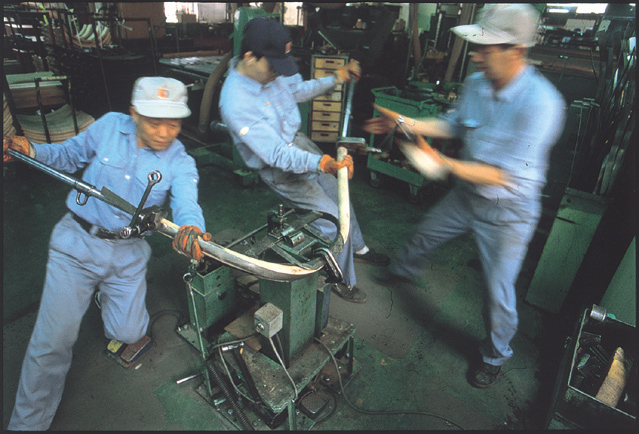
伝統あるトーネット法の曲木技術を伝える。
修業中の若手を指導する飛騨産業㈱の曲木名人、中井正好(左)と澤田明博(右)
「手曲木(マゲキ)加工」
高温で蒸煮し軟化した木材を金型に沿わせながら木を曲げていく加工である。木材が冷めないうちに、曲木成型しなければならないので、作業は時間との勝負になる。木材は樹種によって硬軟様々な特徴を持ち、また木目によっても、曲げる作業の中で微妙な力加減をしたり、曲げるスピードを調整したりと、共同作業で呼吸を合わせ、一本の木を美しく曲げる為には、培われた経験と高い技術が求められる作業である。
木材加工の新技術「曲木」の登場
19世紀ドイツで開発された「曲木」が大量生産を可能にした
椅子の歴史は人間の誕生と共に様々な形に変化し発展してきた。しかし、座り心地の良い椅子を大量に作るためには、手工芸的なやり方では限度があった。そのためには、新しい技術、新しい道具や機械、新しい考えが必要になってくる。
高温で蒸し軟らかくした木材の外側を鉄板で固定し金型に沿わせながら曲げる。型に入れたまま木材を乾燥し、ゆっくり冷ませば狂いを防ぐことができる。デザインによっては、曲げるだけではなくヒネリも加えるなど複雑な加工も可能である。トーネットはこの曲木技術をドイツのウィーンで特許申請し、1842年に認可が下りた。
トーネットの名作椅子№14の後継モデルとして開発され1876年に発売された№18は曲木椅子の基本形ともいえる。すなわち椅子を部材にわけておのおの製造し組み立てるようにしたこと。前脚はホゾで円形の座枠に差し込んで止める構造とし、その座枠は背凭れや後脚と同じように一本の曲木で製作し座面は藤(とう)皮(ひ)の編み込み、さらに椅子の強度を高めるため全ての脚を連結する一本の曲木ヌキを組み合わせるなど構造、技術、造形において完成度の高いものである。各消費地には部材のまま輸送しそこで組立納品された。組立には接着材を使わず、ボルト・ナットと木ネジを用いて固定するノックダウン方式を採用した。このため、大量生産と大量輸送を可能とした。まさに、トーネットの曲木椅子製作方式は現代の製造業のモデルとなる画期的なシステムがこの頃すでに確立されていたのである。
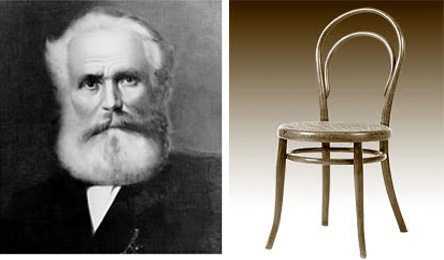
MichaelThonet ミヒャエル・トーネット
1796年〜1871年 ドイツ生まれ。1819年家具工房を開く。1830年積層材を用いた曲木技術の研究を始め、1842年に積層材を使わない無垢材による曲木の特許を得る。この技術で美しい曲木椅子を製造し、高い生産性を実現させた。中でも1859年につくられたNO.14は曲木椅子の名作として名高い。1849年ウィーンに工房を開設し、現在までのトーネット社発展の礎を築く。1856年オーストリア市民権を得る。発明家/企業家の両方において家具を量産するという近代システムの基盤をつくった先駆者である。
先進技術「曲木」の日本導入
日本を代表する「飛騨の家具」は1脚の曲木椅子から始まった
飛騨の豊富な森林資源を生かして曲木家具作りが盛んになったのは、次のような経緯を経ている。
日本では、ドイツ人のミハエル・トーネットが開発した曲木技術を使った最初の家具が明治末期に輸入され、その優美さと優秀さが知られるようになった。当時の日本政府によって民間にこの曲木椅子の製作が奨励され、1906(明治39)年〜1909(明治42)年にドイツ、オーストリアに留学していた農商務省営林技師の佐藤五郎がドイツより十数台のキルヒナー製の曲木機械及び、木工機械を持ち帰ってきており、林業試験場の管轄にあった宮城県の鍛冶谷澤木工所(初代場長は佐藤五郎)に設置した。
明治42年、明治政府は突然外国産の曲木椅子の輸入禁止を命じた。その主たる目的は国内産業の保護と輸出振興であり、国産の曲木椅子業界にとって大きな転換期を迎えていた。
日本における曲木椅子の製造は、1906(明治39)年に東京曲木工場(東京府日暮里)が開業、1907(明治40)年には泉曲木工場(大阪府楠根村)が曲木家具の製作をはじめている。これが我が国における曲木家具製作のはじまりと思われる。
それまでは雑炭か下駄の歯の用途しか無かったブナ材が曲木用材として試みられ、それが適材としての評価を得ると、その技術はブナ材を求めて1911(明治44)年には秋田県湯沢町の秋田木工に、9年後の 1920(大正9)年には飛騨に伝えられ、飛騨産業㈱の前進である中央木工㈱(大正12年に飛騨木工に改称)でブナ材の曲木家具作りが始まった。
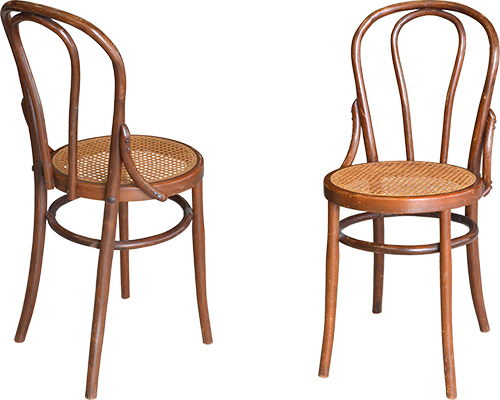
飛騨木工株式会社製 第1号曲木椅子
家具製造技術「曲木」の取組と、技術者・小島班司の活躍
曲木家具製品化の苦労と進展
飛騨地方の曲木技術が飛躍的な発展を遂げたのは、1936(昭和11)年5月30日に飛騨木工㈱に入社した小島班司(当時22歳)の研究指導による貢献に大きなものがある。小島は京都大学農学部の聴講生として在学中には特に曲げ木に魅力を感じ勉強をしていた。
※次は『小島班司。技術開発記録』より転載
◇入社後の活動について
小島班司は入社に当たり清水専務より、「これまでは比較的間違いのない、見よう見まねでやって来た。だがこれからは、君(小島)が基本的・科学的に考え意見をどしどし言って貰い、可能なことから改革して欲しい。」と言われた。所属は一応、工務部研究係とし、研究室を開設するにあたり、「特に曲木班の技術的なことは君の直轄とし、曲木技術の高揚、生産能率の向上をするように。」との要請があった。
1、研究室開設
小島の研究室は工場二階の一隅を与えられ、設計机・製図板・青図焼付台・現像皿・暗室・図面棚・資料棚・図書棚など逐次揃えていった。後日に助手1名が配属された。
◇創業時からの曲木方法の把握と改善
イ)曲木用材
当時の曲木材調達は、飛騨地域周辺のブナ林が多い立木山を購入・伐採・製材し天然乾燥まで山元で行い、それから工場の木材倉庫に貯蔵、三年目頃から用材として使用されていた。いわゆる一貫作業であった。二年間くらいの倉庫貯蔵によって平衡含水率程度は曲木に適当な20%前後となっており合格していた。これにより基準含水率は18%前後とした。
ロ)蒸煮(じょうしゃ)槽と蒸煮
曲木の原理に基づき、最も重要な木材の軟化処理を行う蒸煮槽は、コンクリート作りの集約型であった。材の長短により区分されて収容していた。しかしスチームの圧力は勘で行われていた。そこで吹き込みパイプに圧力計を取り付け2気圧に制限しこれ以内で使用するようにした。蒸煮槽内の上部に水シャワーのパイプを取り付け過乾燥材の場合水で湿らし、それからスチームを吹き込む、またスチームパイプは蒸煮槽下部両側に配置するのは既に実行されていたが、そのスチーム噴射パイプの上にスノコ板を乗せ、下部の材の湯浸けになる過剰の蒸煮を緩和した。蒸煮時間の基準も経験的勘で行われていたのを、使用材の断面に応じた時間を設定した。毎日の作業で出た折損材数をノートに記録させ原因調査の参考とした。
ハ)曲木後の乾燥室
曲木加工後の木材乾燥は、直火式で木炭使用の炉付(W3.6m×D3.6m×H2.5m)程度のもの(同型4室)中央に鉄板の扉(80㎝幅)室内右上の角に排気筒一個、室外右隅に給気口一個体の鉄筋コンクリート製であった。室内の中央部の床は80㎝×80㎝に掘り下げ耐火煉瓦張りとし、下部より熱気を加える構成で床面はロストルを渡していた。乾燥の熱源である木炭は季節に応じ加減(勘)していたが、問題は直火式であるので熱気の上昇下降が急激となり、湿度の高い曲木乾燥には無理があった。また湿度計が無いので室内の温湿度状況は推定するしかなく、毎朝出炉した製品を見て、温度が強かった弱かったと判断し、今日はどうするかと対策をとるという繰り返しであった。強かった時はひび割れが出来、弱かった時は戻り(スプリングバック)が多く再乾燥することになる。直火式乾燥室は熱量を多く消費するものである。改善の一つに先ず鉄板扉の裏にスレート板を張り付け、扉の上部にL字型の温度計を取り付けた。測定は宿直員に依頼し調査記録(時間・温度の変化)を午後6時から2時間毎の計6回取ることにした。この調査結果に基づいて、木炭量、熱気の加減など少々科学的な方法に入ることができ、曲木戻りの防止と再乾燥の減少に効果が上がった。
生産量も増加し、乾燥室も不足となり増設を要することになる。これを機にスチーム加熱、給排気調整可能なものを設計したが一時保留となった。直火式で成果のあがるものとのことで、火炉は中央に、扉は観音開き、製品は二組の担架式トロリーとしトロリーを外部に引き出し、曲木完了のものより積み込み、作業終了と共に乾燥室に送り込む。内部上部排気筒は2個とし外部に給気口(調節付)中央部に炉への給炭口を設けた。宿直員に測温、給気、給炭のタイミング10時・午前1時・・・など(四季に応じて変更)の作業を指示、これにより温度の急上昇を緩和し温度調整のタイミングを考える資料となり、乾燥の改善と作業能率の向上に寄与した。
ニ)折損率の調査
曲木作業中に折損したものは、すぐ隣のボイラーに放り込んでいた。どうして折損したのか、また再利用出来ないか、これは経済的・コストの面からも重大なことであった。材料班から各品種別の納入数と曲木炉より出した製品数の記録をとり、不良数量を検討して材料の取扱を究明した。
曲木に対する簡単な教育がなされていないこともあり、曲木班へは田舎出の力の強い人を配置するという習慣的なこともなかなか改善されず、主力製品は曲木であるという観念を経営者は忘れているようであった。
ブナ材には赤ブナ、白ブナがあり、一般材と異なる偽心材(白太・赤太というものではないという特徴をもち、材全体に水分が分布しているという特殊なものである。製材木取りによってそれぞれに木表・木裏・板目・柾目・追柾となるが、曲げ面は木表または板目にすることが良好であり、蒸煮前に木表面に印をつけてから作業に当たるよう指導した。
蒸煮槽より取り出した材は素早く熱いうちに曲げることが肝要である。先ずは、曲木の原理について勉強することが最も良いことである。
ホ)動力曲木機械の使用で実績向上
1935(昭和10)年アメリカのスロットキン来社の折りに寄贈されたカタログにより、牧野鉄工所で製作したものが曲木工場にあったが、私(小島班司)が入社したときはまだ使用されていなかった。この機械を実用化するよう命令があり、製品№30の折り畳み椅子の台輪と凭れの製作に取りかかった。この機械には既に鉄板製の曲型が取り付けてあった。六本用の当て金でテスト曲げを行うが乾燥して取り出してみるとU字型の曲木の中央部分が尖ったものになり台輪の原図に合致しない、そこで鉄板製曲型は中止し、木材の張り合わせで型を作り原図より中央部を少し平らにしてテストを行った。乾燥してから伸び具合を原図と照合し、具合の悪いところの曲型を削ったり、木片を貼り付けたりし曲型を修正しながらテストを繰り返し漸く完成した。結果は一日6時間稼働で手曲げと比較してみると約5倍の能力となる。毎日統計を取り専務に報告した。機械の偉大さが改めて解ったものである。
※以上『小島班司。技術開発記録』より
曲木にするには木の乾燥加減が難しい。木が乾きすぎると、曲げるときに割れやヒビが入ってしまう。反対に、湿り気が多いと曲げた後、形が元に戻ったり接着部分が離れるなど不良品が続出してしまうなど、この家具づくりが始まったころは商品化するために大変な苦労がありその努力は並大抵ではなかったようだ。
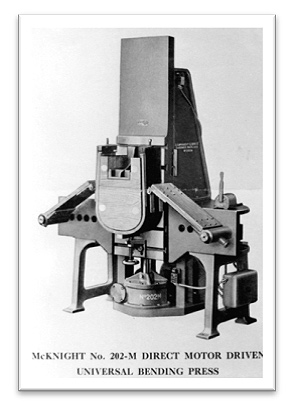
参考にした縦型プレス曲木マシーンのカタログ写真の一つ
へ)商品化と課題克服
失敗に失敗を重ねながら、一つひとつ改良を加えた自信の作を、やっと名古屋の店に初出荷したが、開けてびっくり。商品はラックニスで仕上げた塗装がはげ落ち、みるも無惨な状態であった。高山から名古屋へ荷馬車で4日間、商品を運んでデコボコの山道を運んだのが原因であった。そこで目をつけたのが飛騨伝統の春慶塗。これならコストは高いが、品位もよく堅牢で、しかも地元で入手でき漆塗りの技術者も多くいる。初期の飛騨の曲木家具は漆塗りで仕上げられていた。
こうしてようやく高山での洋家具作りが始まったと伝えられるが、当時の飛騨人の生活様式は、そのほとんどが畳と卓袱台(ちゃぶだい)中心の座る生活であり、普段の生活で椅子に腰を掛けて食事をする・くつろぐという生活スタイルは庶民にとって想像すら出来なかったと思われる時代の中で、洋家具を作ろうとする決断は飛騨の木工産業にとって革新的な出来事であった。
この決断を促した背景には、資源の有効活用という側面もさることながら、平安時代から連綿と受け継がれ、木を知り尽くした「飛騨の匠」の技を持つクラフトマン達の存在が、その挑戦を実現できるという自信にあったことは想像に難くない。
さらに、大正半ば(1920年頃)から始まる大正デモクラシーが日本人のモダニズム受容と住居生活の洋風化を進めるという、まさに生活革命の幕開けが始まった時代でもあったことが飛騨の洋家具造りを進展させることとなった。
1935(昭和10)年頃、飛騨木工(後に飛騨産業㈱に改称)を始め秋田木工、マルニ木工、鳥取木工、東洋木工、東京曲木、松山木工、奈良曲木等が加入した曲木同業者による全国組織の曲木工芸協同組合ができたが、これが出来るまでは各社とも殆ど同型の曲木椅子を作り、安売競争をして互いに自分の身を削り合っていた。

飛騨木工株式会社の曲木家具カタログ
現代の飛騨の匠:小島班司
小島班司(高山市)は当時を振り返って、私は新潟県出身ですが、22才のとき、縁あって飛騨木工㈱に入社した。大学では木材加工の研究に取り組み、テーマは「曲木加工技術」であった。これを企業の中で続けて行けることに魅力を持ち、入社以降木材加工技術の改良・開発に寝食を忘れ没頭してきたが、飛騨人から見れば“よそもん“と言うことで目に見えない壁があり、当初は新しい加工技術を開発してもなかなか現場には受け入れてもらえなかった。その中で、当時の清水専務は良き理解者であり、高周波乾燥機の開発に多額のお金が掛かっても最後まで支援を続けてくれた。私が当時の飛騨産業でやってこれたのも清水専務のおかげと思っている。これからも良い家具造りの為には木を知ることは勿論だが、「木を使うは気を遣う、機械を使うは気を遣う、ことが原点にある。」と、木材の加工技術に青年のような熱い思いを語っていた。
この小島班司こそ、現在の飛騨の家具作りの技術的基礎を築いた最大の功労者として自他共に認める存在であり、特に曲木技術・乾燥技術を初め数々の生産設備などの開発は、飛騨に止まらず日本の木工界に大きな影響を与えてきた。また、彼と共に生産現場で技術改善に挑戦し後世にも伝わる業績を残した職人達の姿は、まさに現代の「飛騨の匠」と言える。

小島班司氏と飛騨の匠らが係わった曲木椅子の数々
製造技術近代化への取組
1936(昭和11)年当時の飛騨木工の生産数量は1万230打(12万2,760脚)と前年に比べ約4割の増産を記録しており、満州をはじめ支邦大陸などにも輸出している。
この頃、特出すべきことは木材中の含水率を測定出来るという携帯式の機器に注目し購入したことにある。当時は、天然乾燥したブナ材をそのまま家具用材として使用しており、このブナ材をさらに蒸気で蒸してから曲木を行っていた。このたっぷり水を含んだブナ材を乾燥するため、直火乾燥が行われており、多量の炭火を起こした部屋にまる一夜ほかりこんで乾かしていたが、どれくらい水分が抜け乾燥したかは、勘に頼るしかなかった。
民間企業初の含水率測定器の購入
ドイツ製の含水率測定器は抵抗式含水率計(シーメンス含水率計)と言い、その購入額は当時の金額にして1,200円もするもので、一軒の家が充分建つほど高価なものであった。この含水率計は京都大学にしかなく、民間の会社(飛騨木工㈱)が購入したのは国内で最初であった。これについて、購入の相談をしに行ったところ田舎の会社が分不相応で色気を出しすぎと言われ担当者はガッカリして帰ってきたという。しかし経験と勘に頼るしかなかった当時の木材乾燥は、含水率測定という新しい技法の登場により、以降の木材管理技術の飛躍的向上と高品質の家具づくりを可能にしていった。
ルーターマシンの開発
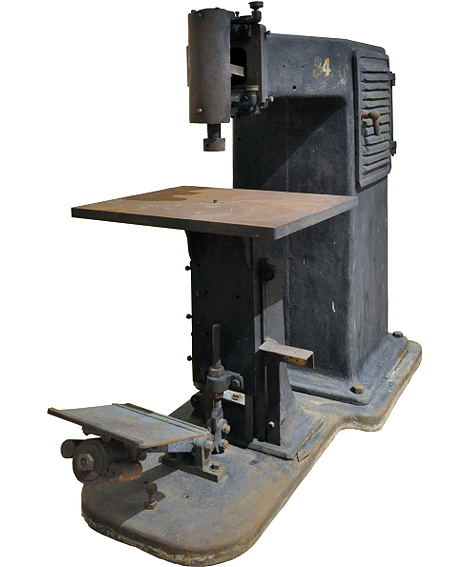
飛騨木工株式会社製作による国産第1号のルーターマシン
1937(昭和12)年には米国輸出に力を入れると共に、米国家具業界の視察や製造技術の研究のため幹部を派遣していた。
渡米中に現地の家具工場視察で当時の新鋭機であるルーターマシン(Router)を見てきたことから、これを参考にして飛騨木工㈱製作による国産第1号のルーターマシンを開発した。
一番苦心したのは高速回転モーター(10,000回転/分)と切削軸をつなぐベルトの研究であり、試行錯誤の末、考えついたのが畳縁(麻布製)で作ったベルトの開発である。この発見がこの機械の実用化につながった。このルーターマシンは日本国内で初めて実用化された第1号機の誕生である。
太平洋戦争時代「木工技術の活用」
戦時中は軍需品の製造・木製飛行機も試作
1941(昭和16)年12月、太平洋戦争に突入、生産内容も弾薬箱や用具箱といった軍需品生産の比重が大幅に増えていった。1943(昭和18)年10月には軍需省より木製戦闘機の生産が内命された。戦況が悪化するなかで、あらゆる物資にも困窮を極め、航空機に必要な軽合金にも不足をきたすことが予測され、日本陸軍は現用機、試作機のいかんを問わず、木材での代用を考慮せざるを得なくなった。「大東亜決戦機」として期待された四式戦「疾風」(中島キ−84)もその対象となり、機体構造の大部分を木製化することになり、1942(昭和17)年頃から立川飛行機はその設計に取りかかっていた。
飛騨木工㈱は立川飛行機㈱の指導で木製戦闘機(キ−106)の機体の製作を担当することになり、胴体、主翼骨組みなどは当時自社で製造していたベニヤ板(合板)製作の技術を基に、ヒノキやブナの単板を積層したものを使用するなど、飛行機の軽量化に苦心していた。軽量化のために様々な工夫がなされたが、その工夫の一つに、座席下の床材にジュラルミンの代わりにブナ単板を網代(あじろ)編みしたシートが作られた。単板組されたシートは滑らず強くて軽いことと、安定供給が出来るという優れたものであった。

岐阜県立高山工業高校製作高山航空工業㈱で製造していた
木製飛行機「キ-106」の1/6スケール模型
ところで、木製戦闘機は終戦までに全国で試作機を含め計10機が完成しているが、テスト飛行の結果は、期待された性能に届かず、さらに研究を続ける事となったが終戦を迎えると同時に断ち切れとなった。
鉄工所(班)社内に開設
当時の工場では、機械加工に必要な刃物の研磨や小物修理は職場毎で行っていたが、少し大事なものは社外の鉄工所に頼んでいた。
1943(昭和18)年、市内の牧野鉄工所の主・牧野義一氏が鉄工所設備を持って飛騨木工㈱に入社してきた。これを機に鉄工班を編制、班長を古滝利雄氏とし旋盤工その他若干名で出発した。これにより工場の設備全般の保全改修に亘り利用度が多くなり、さらに専用機の自社製作も出来るなど、その効果は大きなものであった。
技術革新と曲木技術の近代化
1946(昭和21)年にはGHQ(連合軍総司令部)から駐留軍兵舎・宿舎に使用するダイニングセットなどの大量注文が入り、増産と品質の向上、さらに生産技術の開発に力を注ぐ必要があった。
日本初高周波電波乾燥機の開発とその実用化
1947(昭和22)年には、前出の小島班司(当時工場長)が、不良導体に通電中に発熱するヒントから木材加工技術への応用を考案し、国産実用化第1号の出力1kwの高周波電波乾燥機(radio heater)の開発とその実用化(水冷式・出力20kw)に成功、飛躍的な曲木乾燥の発展と木材接着方法にも技術革新をもたらした。
を利用した曲木乾燥.jpg)
木工業界初のラジオヒーター(高周波発信器)を利用した曲木乾燥
対米輸出再開と技術改善への新たな挑戦
1949(昭和24)年、対米輸出を再開する。戦後初めて木製折畳椅子(#1001)をアメリカへ輸出した。
第1回目の出荷は360脚で、売価は19万3,380円、為替レートは1ドル550円であった。米輸出も順調にスタートしたが、試験的に船積みしたコロニアルタイプの椅子は、現地で取り出してみるとシートの接着に亀裂が入り、丸いはずだった椅子の背もたれのホゾは楕円に変形しているなど、完成品として輸出していた折畳椅子の経験では考えられない惨憺たる状況であった。
最大の原因は、梱包に使用した木箱の材料には生材のままの針葉樹(姫小松)が使われておりその材料に含まれている水分が船積され二週間以上かけて太平洋を横断する内に製品に吸収されるという事にあり、あらためて木材の水分管理の重要性を思い知らされることとなった。
インターナルファン式木材人工乾燥機の開発
同機の実用化前年、木材の人工乾燥による含水調整を目的としたインターナルファン式の強制循環式木材乾燥装置(Forced Circulation Type)が完成し運転を始めており、温湿度調節が容易で乾燥ムラが少なく、品質の安定化に威力を発揮するこの乾燥装置を持っていたことが、木材の乾燥不足による含水不良の原因をクリヤーできる原動力となった。当時一般的には、直接燃焼瓦斯方式(Direct Furnace Type)といわれる燻煙式の乾燥方法が普及していたが、温湿度の調整が困難なため乾燥された木材の含水率はバラツキが多く、家具用材として最適な含水率に達した材料確保にも相当苦労していた。
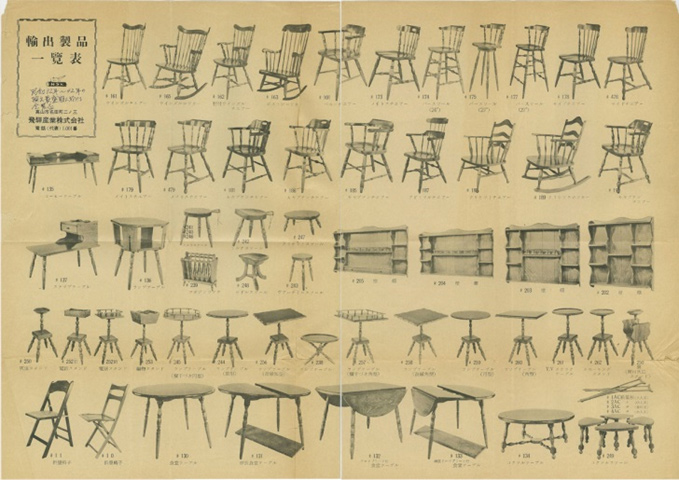
対米輸出製品一覧表
大量生産時代に対応する高性能マシーンの開発
昭和30年代前半には総販売額3億43百万円の80.3%が対米輸出となり、主力商品であるコロニアルチェアー(キャプテンチェアーだけでも5万脚)の生産は自社だけではバイヤーの注文に応じきれず、以前から少しずつ国内向けにロクロを使って南京椅子を作り始めていた柏木工㈱にウィンザーチェアーの製造を依頼すると同時に、飛騨産業からの技術指導が始まっている。
自動サドルシートマシンの開発
当時、米国には凹面を削り出すサドルシートマシンはあったが、加工は二回削りの工程が必要であった。これを、一回の加工で削り出すことのできるよう、新たな専用機を独自に開発するための研究を開始した。指定された凹部の深さと凹部の平面形状を削り出すための刃物(カッター)の型や、このカッターを自動的に上下させるためのカムと、凹部の複雑な削り形状にカムの動きを制御するガイド板の工夫など、さまざまな技術的問題を克服しながら、ようやく完成することが出来た。これは日本、いや世界でも初の専用機であるといえる。
多軸ボール盤の製作
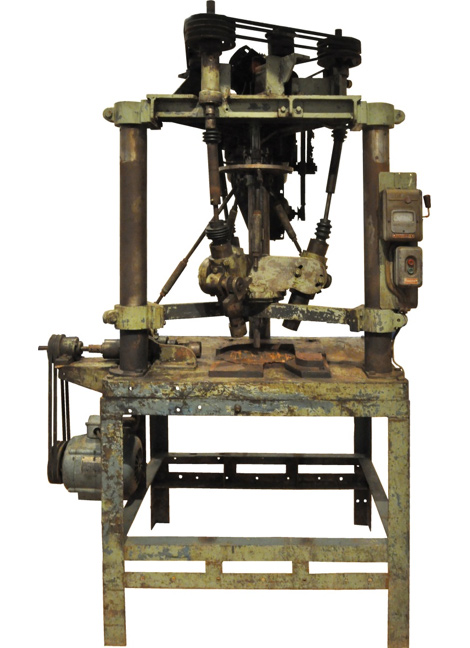
コロニアルチェアーのシートの表面には、背凭れや肘受けになるスピンドル、裏面には脚のスピンドルを取り付ける孔明けを必要とする。それぞれの孔は、孔明角度、孔明方向も一定でなく、一個々を加工していたのでは一枚のシートの孔明けの数もたくさんあり手間がかかりすぎる。この上下の孔明けを一挙に行う機械装置は、表面の孔明け加工にはフレキシブルシャフトとの連動により行い、裏面の脚孔加工はシリンドリカルモーターにて行うようにした。上下軸ともに傾斜角度を自由に調整出来るようにしてあるのが最大の特徴である。この装置の製作により、加工は正確にしかも早く生産出来ようになり能率は向上した。
自動ロクロ加工機の製作
また、このころ、米国から入手した機械カタログの中に、スパイラルカッティング方式のロクロ加工機が紹介されていたのを参考にして、自社鉄工所でロクロ加工機第1号を製作、この時習得したロクロ切削のための加工技術が後に迎えるコロニアルチェアーのロクロ部品の大量生産時代に生かされることとなった。また、このロクロ機は、スポーツ用品を製作しているミズノの養老工場からも強い懇願があり、特別に数台を製作、野球の木製バットを作るため納められたこのロクロ機は、現在も当時のままの姿で現役稼働している。
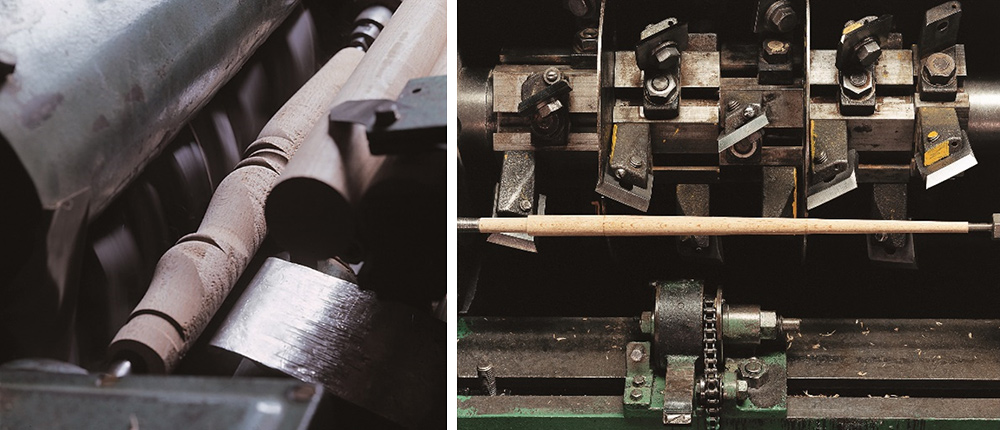
飛騨産業の自社鉄工所で製作した第1号ロクロ加工機と刃物セットの状態
自動倣面取盤の製作
1957(昭和32)年11月18日に完成した自動倣面取盤(アメリカカタログ参考)は、コロニアル生産の専用機の一つである。当時はまだ国産機はなく欧米においては既に実用化されていた。自社製に取り組んだが一番困難な問題は座板の木目の縦方向二面と木口方向二面の切削であった。縦方向二面は速度を速く、木口方向二面は遅くと無段階的に調整できる機構をどのようにするかの工夫が必要であった。
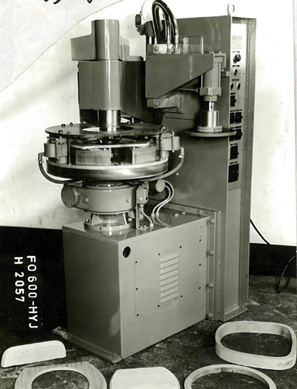
自動倣面取盤製作の参考にしたアメリカのカタログ
我が国の発展途上期は輸出で貢献
昭和30年代半ばには87%が輸出と、そのピークを迎える一方、空前の消費ブームに沸く国内市場向けに開発したモダンな家具(C−60、ホームセット・#715、サロンセット・C−66、食堂セット)にも人気が集まり、その生産にも力を入れなければならなかった。1946(昭和21)年に創業した日進木工㈱は、このころ炬燵櫓及び整理ダンスなどの製造販売を手がけていたが、飛騨産業の国内市場向けモダン家具の製造の一部を引き受けることになり、椅子の加工技術の殆どを飛騨産業から習得していくことになった。
このようにして、飛騨が日本国内の脚物家具における代表的な産地として形成される基盤づくりが始まった訳で、この昭和30年代の輸出の拡大による生産供給の対応が、今日の両社の企業カラーを決定することになるとは、当時は想像すら出来なかった。
高度成長期からは内需拡大へ方向転換
昭和30年代後半、それまで順調に推移してきた輸出も鈍化し始め、益々国内販売に力を入れることとなったが、39年の東京オリンピック、昭和40年代前半の“いざなぎ景気”に支えられて、飛騨の各社とも国内需要に急成長を遂げていった。
昭和40年代の流通は百貨店がその中心的存在であり、家具の販売にとどまらず生活提案として家具・インテリアを始め、数々の生活用品の実験的提案を行うなど、消費者の生活意識の向上に果たす役割を担っていた。高島屋の設計部、伊勢丹の研究所などに代表されるインテリア部門は、その企画力と共に家具メーカーにも大きな影響を与え、量より質への意識転換と日本人のための“より好ましい生活空間の設計”(高島屋、シャンブル・シャルマント展の基本テーマ)にオリジナル家具の開発を数多く手掛けており、当時デザイン開発された内の幾つかは飛騨産業でも作り続けられており、発売以降30数年経た今でも、現代の生活環境に機能的・デザイン的にも納得できる家具として多くのファンを持ち続けている。
昭和50年代に入ると、作れば売れる時代から、自分らしくいい物を選択するという、消費者の生活意識の変化を受け、新しい住まいの提案、家具と生活への提案を積極的に行うようになってきた。このころから漸く日本の家具といえるデザインを通じて、生活文化をより豊かにという意識が始まったといえる。
現在、飛騨は脚物家具において全国に類を見ない一大産地を形成するに至り、その企業数も48社、年間出荷総額は約225億2千万円となっている。
民芸に造詣が深く飛騨をこよなく愛し続けてきた花森安治氏は、これを機に「飛騨の家具」と匠を称える色紙2枚を飛騨産業に贈った。飛騨産業は、この「飛騨の家具」と花森氏の書いた文字そのままを使い、ブランドとして全商品に赤色タッグ表示したことから始まっており、当時の旅行ブームに火をつけたDiscover japanによる飛騨ブームにも相まって全国に「飛騨の家具」ブランドを浸透させた貢献は多大なるものがある。
協同組合飛騨木工連合会の歴史概要
飛騨高山の木工業界における団体結成は、1950(昭和25)年に高山木工会としての親睦団体がつくられたことに始まる。1974(昭和49)年ころには高度成長も終息し各社とも低成長時代の模索が始まったが、この時飛騨一円の業界の連携を更に密にして、厳しい時代に共存共栄の理念で邁進すべく、岐阜県木工連合会飛騨支部と一体化し、昭和49年10月に協同組合飛騨木工連合会に発展的に統合改組し、来るべき新時代へのスタートを切った。爾来5年間は低成長の苦しい時期だったが、当地方の会員各位は、それぞれ懸命な自浄努力による減量経営を実践し、また生産内容の改革や新商品開発を積極的に取り組み、少数の脱落者はあったが、木製品生産地として、日本全国に名を馳せている。木工会発足当時の1950(昭和25)年の年間生産額は約2億円であったが、1979(昭和54)年の高山の出荷額だけでも推定2百億円を超える額になっている。
昭和50年代半ば以降の10年間は、日本経済安定成長期の中で、ダイニング家具が一般家庭に普及していく需要拡大の中で発展をしてきた。飛騨の家具はデザインと品質の良さにより、市場での高い評価を得て、家具産地としての地位を獲得してきたといえよう。
1983(昭和58)年以降、行政の支援を受けながら、組合が総力を挙げて大消費地の東京や大阪で開催してきた積極的なイベント(飛騨家具新作展)が、「飛騨の家具」ブランドをより高め、発展の基盤を築いていった取り組みであった。
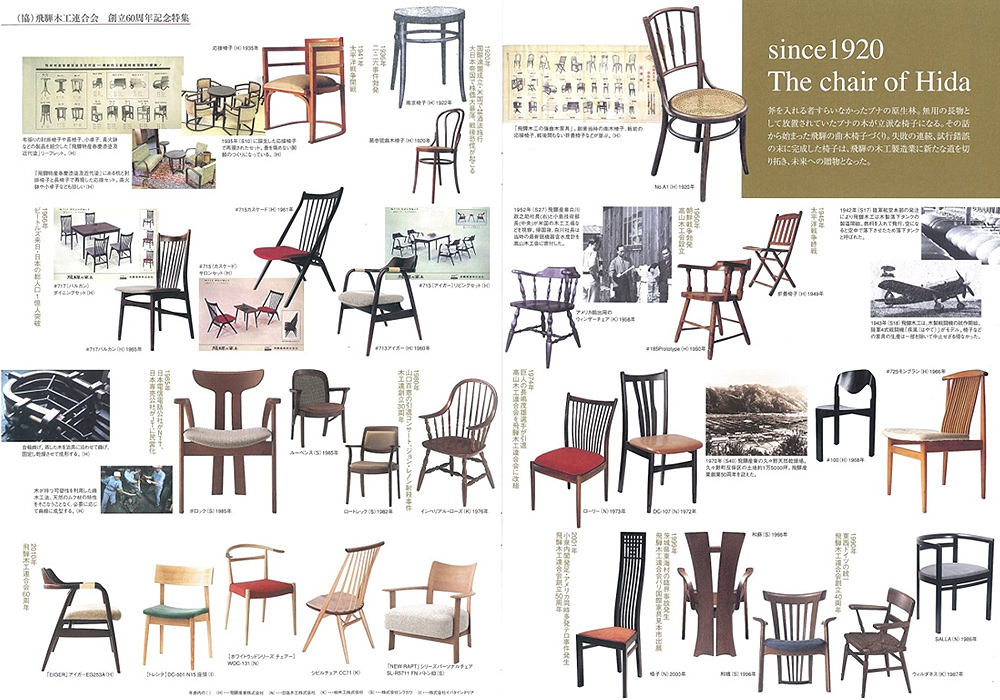
飛騨の家具メーカー製品の現代までの変遷
[飛騨一市三郡の最盛期家具装備品出荷額]
1991(平成3)年の年間総生産額:384億50百万円 従業員数:2,812人
ところが、1991(平成3)年から始まったバブル経済の破綻による「平成不況」の長期化により、日本のあらゆる産業の需要停滞や減少を引き起こし、更には円高で、輸入品の浸透による価格破壊の波が押し寄せてきて、日本経済の構造変革を根底から促すようになった。つまり、生産形態・流通形態・販売形態など、変化に対応できない企業の淘汰が始まった時代といえる。この時流が家具業界にも現れ、多くの企業の倒産・転廃業があった。飛騨の家具業界においてもこの大きな変革の嵐は避けられず、2018(平成30)年現在では組合会員数22社・年間総生産額126億44百万円・従業員数1,318人となって、ピーク時に比べ大幅に減少している。
この逆風が続く中で1990(平成2)年からは、今まで需要開拓推進事業として過去4回、隔年ごとに大消費地である東京(3回)大阪(1回)で大型展示会を行ってきたが、生産地である地元高山で開催することになり現在「飛騨の家具フェスティバル」として毎年9月(令和2年度は10月24日~28日)に開催され国内有数の産地展示会として今日まで続いている。現在も椅子の生産を主流とし、ダイニングチェアでは全国一の出荷量を誇っている。
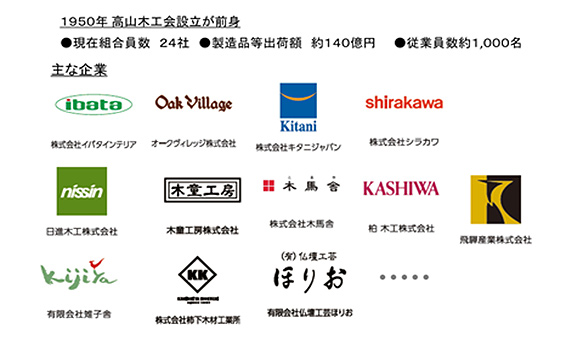
飛騨木工連合会の家具製造企業会員(2020年現在)
日本の主要家具産地
わが国には家具の五大産地(旭川・静岡・飛騨・府中・大川)がある。
飛騨以外はタンスや鏡台づくりから始まった産地であり、椅子の産地といえるのは飛騨・高山だけである。現在では椅子を中心にテーブルやボード類(箱物)などもコーディネート開発し、ワンルーム&ワンハウス全ての家具をトータルに提案している。全ての家具づくりに対応できる技術力をベースに、ますますグローバリズムが進展する現代社会に、潤いと癒しのあるソフトな生活提案とクオリティーの高い家具づくりを発信し続けたいと考えている。
【飛騨家具以外、日本の主要な家具産地】

旭川家具(主に旭川・東川・東神楽錦江地区の総称)
明治の頃、国策による北海道への大量移住に伴って道内の家具の需要が増え、全国の家具建具職人もそれに伴い移住してきたことから始まる。豊富な森林資源があることも旭川の強みである。また現在では3年に一度開催される家具トリエンナーレ「国際家具デザインフェアー旭川(IFDA)」(1990(平成2)年より開催)では世界レベルのデザインコンペティションを実施して、デザインの質の向上を追求している。

静岡家具(主に静岡市・島田市・焼津市・藤枝市)
徳川家光公の時代より職人が集まり定住するようになる。豊富な森林資源に恵まれた静岡の立地を生かし、漆器作りで培われた伝統技術を洋家具である鏡台に活用する。以後、鏡台の生産に注力しながらも茶ダンス・桐ダンス・仏壇などの大型家具にも分化していった。今では製造問屋を中心に生産から販売までを分業して行う静岡特有の形態になる。

府中家具(主に広島県府中市を中心とした地区)
宝永年間に円山円造が大阪で箪笥の製法を習得し、帰郷後製作に着手したのが始まり。大正時代には箪笥職人が軒を連ねるようになる。戦後「婚礼家具セット」を他産地より早く開発し爆発的なヒットを生む。現在でも箪笥を中心とした収納家具の産地であり中・高級家具を手がけ提供している。
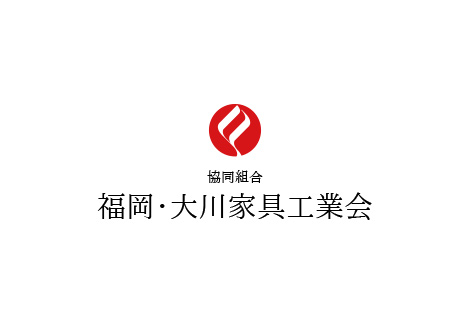
大川家具(福岡県大川市を中心に隣接する県まで広がる)
約470年前に船大工の技術を生かして生まれた指物家具に端を発し今日に至る。現在では箪笥・食器棚を中心とした日本最大の家具産地として成長し、高級家具から普及品まで幅広く生産し、住宅関連産業も含めたトータルインテリア産業へと発展し、量産家具を得意としている。隣接の佐賀県諸富町へも広がりをみせている。
日本の代表的家具産地
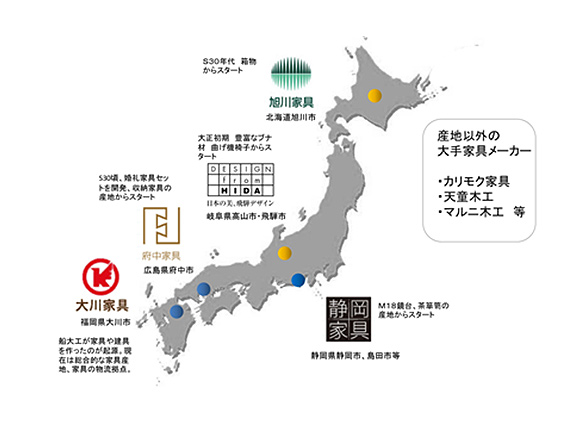
飛騨から世界へ 匠の心と技を受け継いで
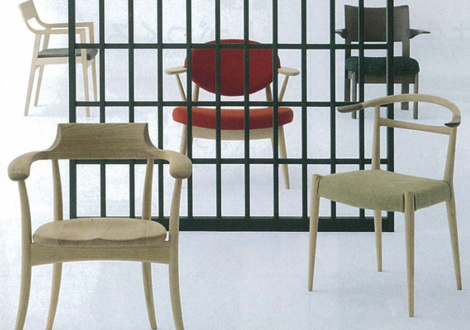
「飛騨の家具」は飛騨デザイン憲章に基づいたモノづくりを目指している。
このデザイン憲章は、私たちにとって自己啓発の一環でもあり、まだまだ大輪の花は咲いていないが、多様な枝葉は確実に伸びている。また、各社、各分野で、デザイン憲章に対する受け止め方に違いはあるが、それはむしろデザイン憲章の内容が育ってきている証拠でもある。
私たちは、先人が育んできた技と精神を基盤として、世界の人々に愛される飛騨デザインの創造を目指している。そして、それぞれの企業や個人がお互いを尊重して個性を磨き競い合うことが、地域社会の発展と人々の幸福につながるものと信じて、「飛騨の家具」の基本理念として、飛騨デザイン憲章を 1998(平成10)年8月1日に制定・宣言した。
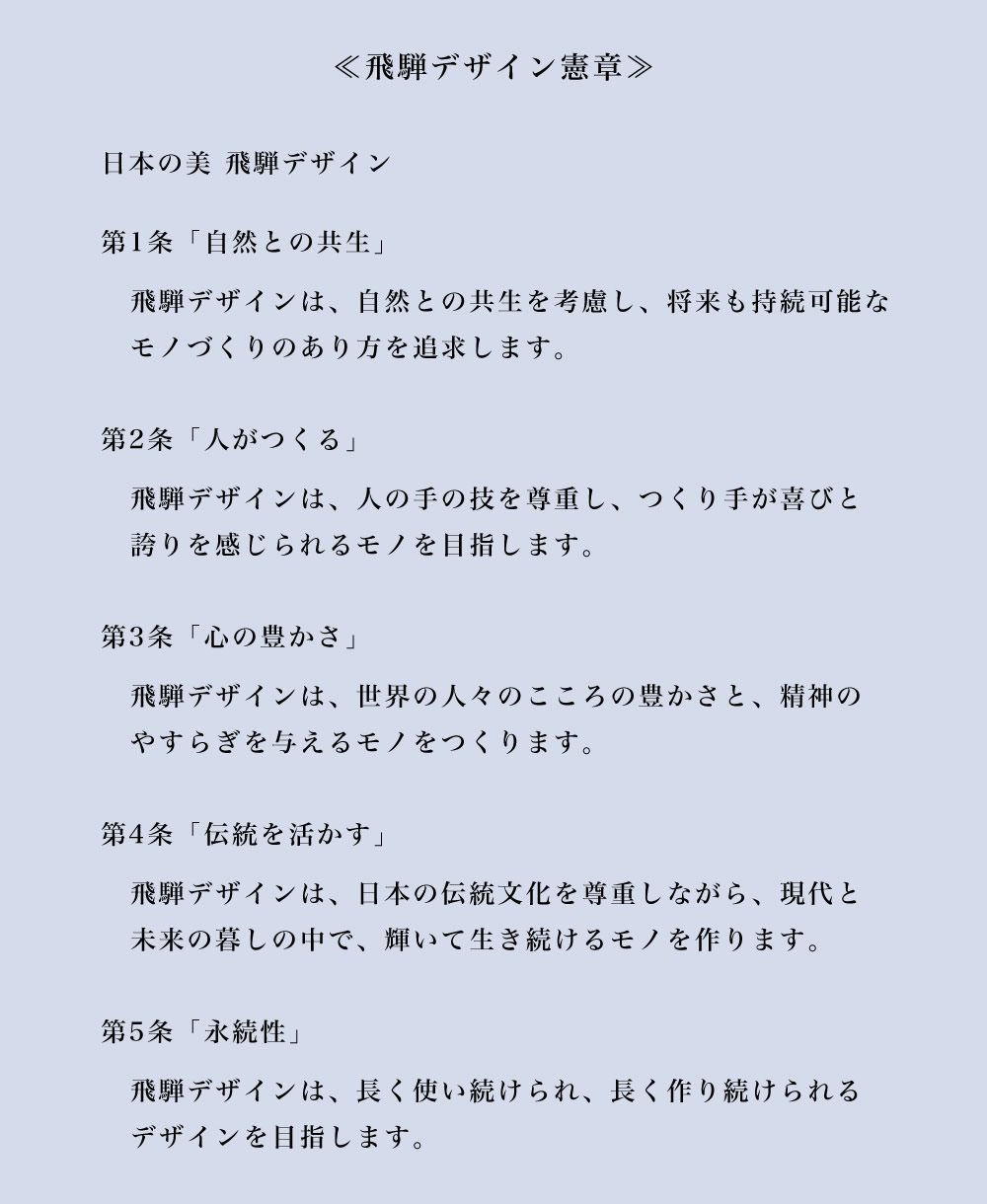
【飛騨デザイン憲章】
飛騨デザイン憲章とは、飛騨のランドマークである。「日本の美 飛騨デザイン」というテーマと五つの条文を掲げ、世界に向かって、日本を代表するデザインを発信している。千数百年もの間、飛騨の匠が脈々と受け継いできた技と魂。現代の匠たちはその伝統を活かし、伝統を超えた更なるモノづくりに挑んでいる。
新世紀を迎えた今日、私たちは自然との共生を図り、資源の活用と再生を循環し、心の豊かさと感動のあるモノとの関係を築いていかなければならない。飛騨の地で木工を生業とする全ての人たちが、高らかに宣言した飛騨デザイン憲章。それは未来に向かって謳う木匠たちの飛騨スピリットなのです。
.jpg)
※デザイン憲章の序文
「飛騨の家具」ブランド化への取組
飛騨産業株式会社固有のブランドとして半世紀あまり使用されてきた図形商標「飛騨の家具」を、地場産業振興に役立つためならばと、地域ブランドとして協同組合飛騨木工連合会が使用することを飛騨産業株式会社:社長 岡田贊三が地域団体商標として使用を許可したことで「飛騨の家具」ブランド化への取り組みは始まった。
.gif)
飛騨産業㈱図形登録商標 「飛騨の家具」|文字デザイン:花森安治(暮らしの手帖社)
飛騨木工連合会が「飛騨の家具」を地域団体商標として登録する必要性を感じたのは、海外からの輸入品などに「飛騨の家具」という名称をつけて販売したり、小売店などがむやみに「飛騨の家具」という言葉を使用したフェアなどの販売行為をしたりすることが横行し始めていたことや、中国をはじめとするアジア諸国から低価格の家具が大量に輸入され、国内の業界には逆風が吹き始めていたことがあげられる。飛騨木工連合会は競争力の強い魅力ある製品づくりを実現するため「中国やアジア諸国の製品とは一線を画して、価格競争に巻き込まれないような質の高い家具づくりを目指そう」と方針を明確にした。同時に、輸入家具などに勝手に「飛騨の家具」という名称を使わせないために地域団体商標の取得に踏み切り、2008(平成20)年1月に登録にこぎつけた。
そのころ、中国で日本の各地の地名が「商標」として登録されるという問題が取りざたされていたため、2009(平成21)年5月には台湾で、2010(平成22)年4月には中国で「飛騨家具」「飛騨・高山家具」の商標を登録した。
これで、外部の業者に「飛騨の家具」という表記を勝手に使わせないという守りは固めたが、これだけでは消費者からの評価を高めることはできない。飛騨の家具がほかの産地で作られた家具よりいかに優れているかを消費者に知ってもらわなければ、家具販売の競争には勝てないからだ。そこで、商標取得と並行して「飛騨の家具」の認証基準要項の策定に取りかかった。その基準はエコロジー、産地、保証、品質、木材、デザインの六つの分野から構成されている。
- 飛騨の家具認証基準
- 1,エコロジー基準
地球環境、地域環境、健康に配慮した資材や原材料の使用及び製造方法に取り組んでいる組合員企業が製造した家具であること。
2,産地基準
協同組合飛騨木工連合会の組合員企業が製造した家具であり、製品の木部加工(木取り加工終了後から開始される木部加工)が飛騨地域内で全て行われている家具であること。
3,保証基準
協同組合飛騨木工連合会が認定した明確な保証基準書が、添付されているとともに、木部の保証期間が10年間保証となる家具であること。
4,品質基準
品質に関わる法律を遵守するとともに、協同組合飛騨木工連合会が認定した「表示文、警告文、取扱説明書」等が添付されている家具であること。
5,木材基準
飛騨の匠の時代から受け継がれている「木材に対する優れた目利きの技術」により選ばれた、良質な木材を使用している家具であること。
6,デザイン基準
飛騨デザイン憲章を遵守している組合員企業が製造した家具であること。

※二つのロゴマークは2009(平成21)年11月付で商標登録済み。

飛騨木工連合会:会員各企業の製品
飛騨地区を代表する家具メーカーの紹介
飛騨産業株式会社 品名 [KISARAGI]
柏木工株式会社 品名 [BOSS STYLE]
株式会社シラカワ 品名 [伸空]
そんな小さな可愛い手を高く上げた立ち姿がチェアのバックの構成となっています。子供の表情を揺らぎの面の流れに生かし、自由奔放に振る舞う姿を表現しました。伸空と桜水は直線と曲線でデザインされていて、面のとりかたなどを似せ、姉妹の様なニュアンスを表現しています。
日進木工株式会社 品名 [WHITE WOOD]
株式会社イバタインテリア 品名 [Humming]
※1968年飛騨産業㈱は人間国宝・黒田辰秋氏指導のもとに
椅子30脚・卓子10脚・花3台脚を新宮殿“千草・千鳥の間”に謹製納入。
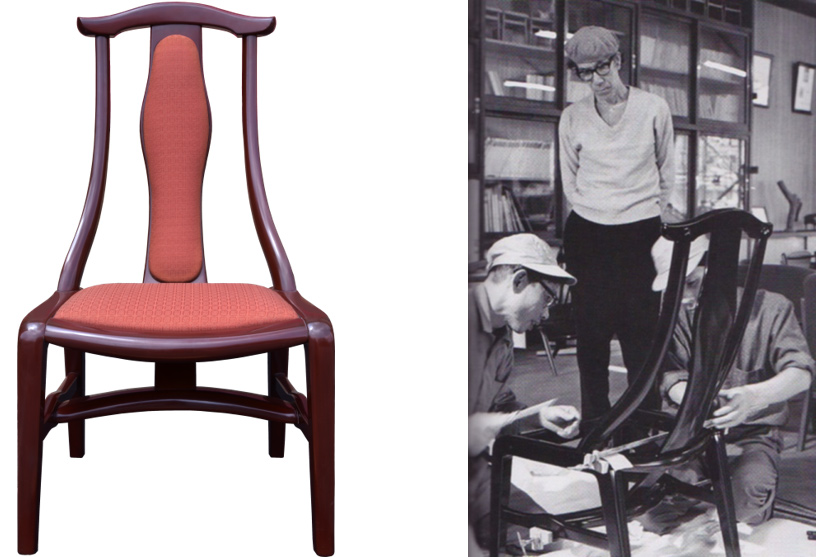
「飛騨の家具」新たな挑戦
受け継がれる匠の伝統
飛騨の家具の老舗である飛騨産業㈱の例を紹介する。飛騨産業㈱は、外部の文化の受容や新しいものを開発していく進取の気性が、しかも匠の技術分野で、飛騨はいまなお脈々と息づいていることを強く実感させる企業なのです。
【業界タブーへの挑戦】
最初に不思議に思ったのは、家具に少しでも節(ふし)が入っていると不良品あつかいされる。わずかな節があるだけで不良品となったものが、山積みになっている。資源の有効な活用に相反する無駄遣いの現状があった。これを何とか生かして家具をつくれないか。就任間もない飛騨産業㈱の社長岡田贊三はすぐさま家具デザイナーに相談すると、デザイナー佐々木敏光は節入り高級家具の開発にすぐさま反応した。
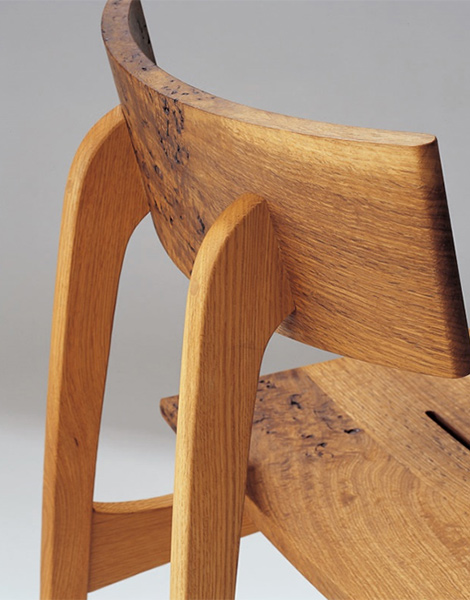
しばらくしてフォルムにクラフトの要素を融合した、日本的なデザインのスケッチが送られてきた。そのときに「これはいける」との手応えを感じ「節を活かした家具づくり」が始まった。すぐにホワイトオークなど広葉樹材の節を活かした家具をつくり商品化したところ、またたく間に全国的な評価と評判を得た。
日本各地で都市化が極度に進むなか、一方ではオーガニックや自然素材を大事にする「ナチュラル志向」な人々が増えてきたことや、材料に節があるため他の材料に比べて手頃な価格が付けられたことが大きな価値観をもたらすことになった。従来からの技術の高さと優れたデザインによって、安物のイメージを脱し、高級品イメージとして広まっていった。
生産工場のあちこちで社員たちが板材の節を磨いている。物がひっかからないように、一個々を指で触って確認しながら丁寧に磨いている。一枚の板だけでも節はいくつもあり、それが模様ともなるので、家具には一つとして同じものがない。「自然の造形美を活かしている」それがこの家具の大きな魅力の一つであり、業界の常識を疑ってみたことがこの家具の出発点であった。
【国産針葉樹(スギ材)の活用】
日本には杉の木が溢れるほどたくさんあって大きな問題となっている。スギ花粉は花粉症を発症する、国民的な病までになっている。戦後全国の里山に植林された杉は、木材として活用できるまでに育ってきたが、用途の無いまま手入れもされず山中に放置され、雑草も生えない死の山と化している。杉の林をなくして広葉樹林に戻さなければならない」豊かな水や国土を守るためにも重要な課題である。杉の木は木材として優れているから、別に杉畑をつくることも必要だ。ただ杉の木は柔らかくて傷が付きやすいため、建材や椅子・テーブルなどには不向きとされてきた。飛騨産業はこの問題にも挑戦している。
飛騨産業㈱では、岐阜大学農学部名誉教授・棚橋光彦氏(現:きつつき森の研究所相談役)が研究開発した「杉の圧縮・固定方法」を取り入れ「杉の圧縮固定装置」を開発、平成16年10月から本格生産を開始している。この設備では杉の木を最大で60〜70%も圧縮できる。
圧縮工場では、飛騨の山々から伐採された杉丸太が沢山積まれている。これを製材して圧縮用の板材がつくられるが、圧縮材には板目材が最も適しているという。乾燥された板材を圧縮し易いよう木材を蒸気風呂で蒸して木材を柔らかくする。この材料を温かいうちに圧縮機にセットしプレス圧をかけて木材を目的の厚さまで圧縮してようやく完成する。これで杉材はきわめて堅牢となり、傷がつきにくくなることはもちろん、広葉樹並の優良素材へと変身を遂げている。
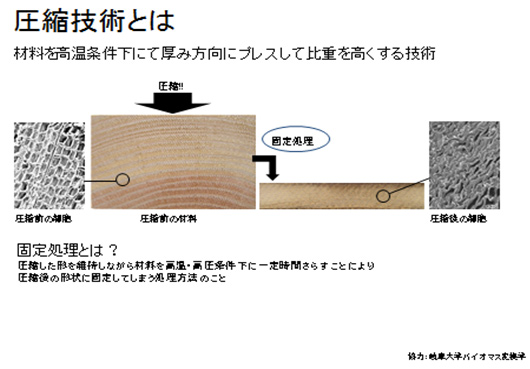
【杉材の枝葉の新たな活用】
さらに飛騨産業㈱は、一本の木を全て無駄なく利用することにも取り組んでいる。新しい試みは「樹木の枝葉」の活用である。木材の伐採現場では、木材の枝葉は山のゴミのような扱いで、伐採現場に大量に放置されたままである。大雨の時など、この枝葉を含む残材が山中から流れだし人里に堆積し甚大な被害を発する元凶となっている。
この枝葉が持つ秘められた成分を棚橋光彦氏が開発した独自の方法・高圧水蒸気圧搾蒸留法(特許取得済み)で樹液抽出することで、環境に優しい新しい資源としての科学研究にも取り組んでおり、森林資源を農業と結びつける試みとして大きな成果を上げている。
この蒸留方法は、原材料を高圧水蒸気下でプレスし精油や蒸留水を抽出するものであり、通常の水蒸気蒸留法では得ることの出来ない貴重な成分の抽出が可能となる。抽出した蒸留水は、100%天然由来の植物活性液として農産物成育関係の分野でめざましい成果をもたらしている。林業の資源を活用して農業が潤うという画期的な連携が実現しつつある。
このように、飛騨は常に新しい価値の創造や、新しいものの開発に積極的に取り組んできている。飛騨の匠の伝統が、現代の飛騨の匠のチャレンジ精神へ、しっかりと受け継がれていることを強く感じさせ、さらに世界へ発信することができる飛騨のものづくりのこだわりがここにはある。
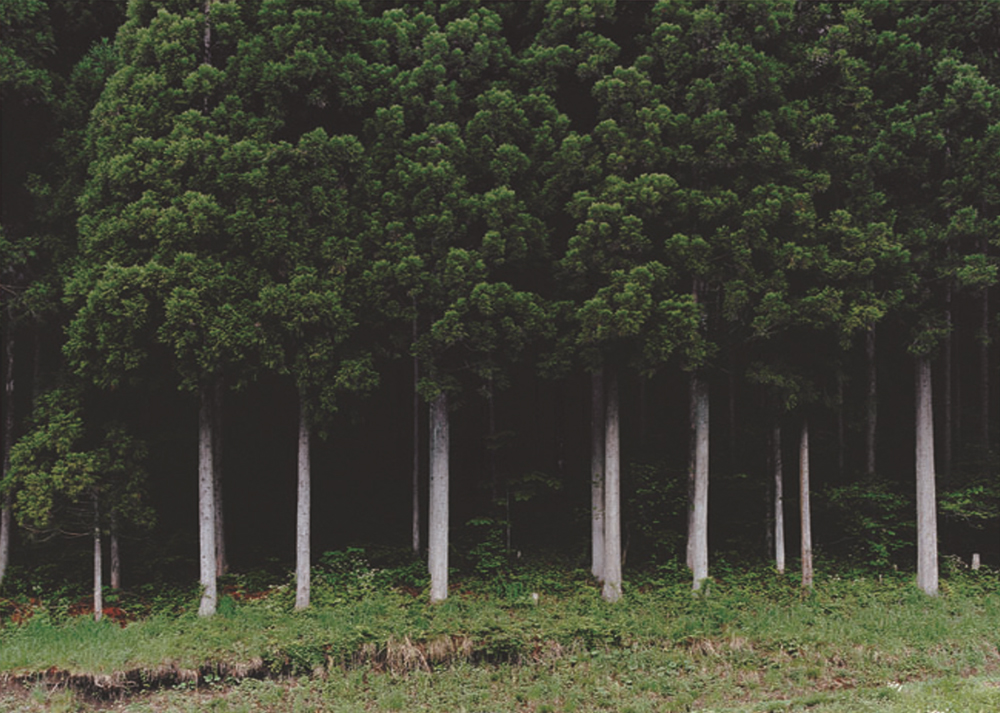
森と共にあゆむ:里山の杉林